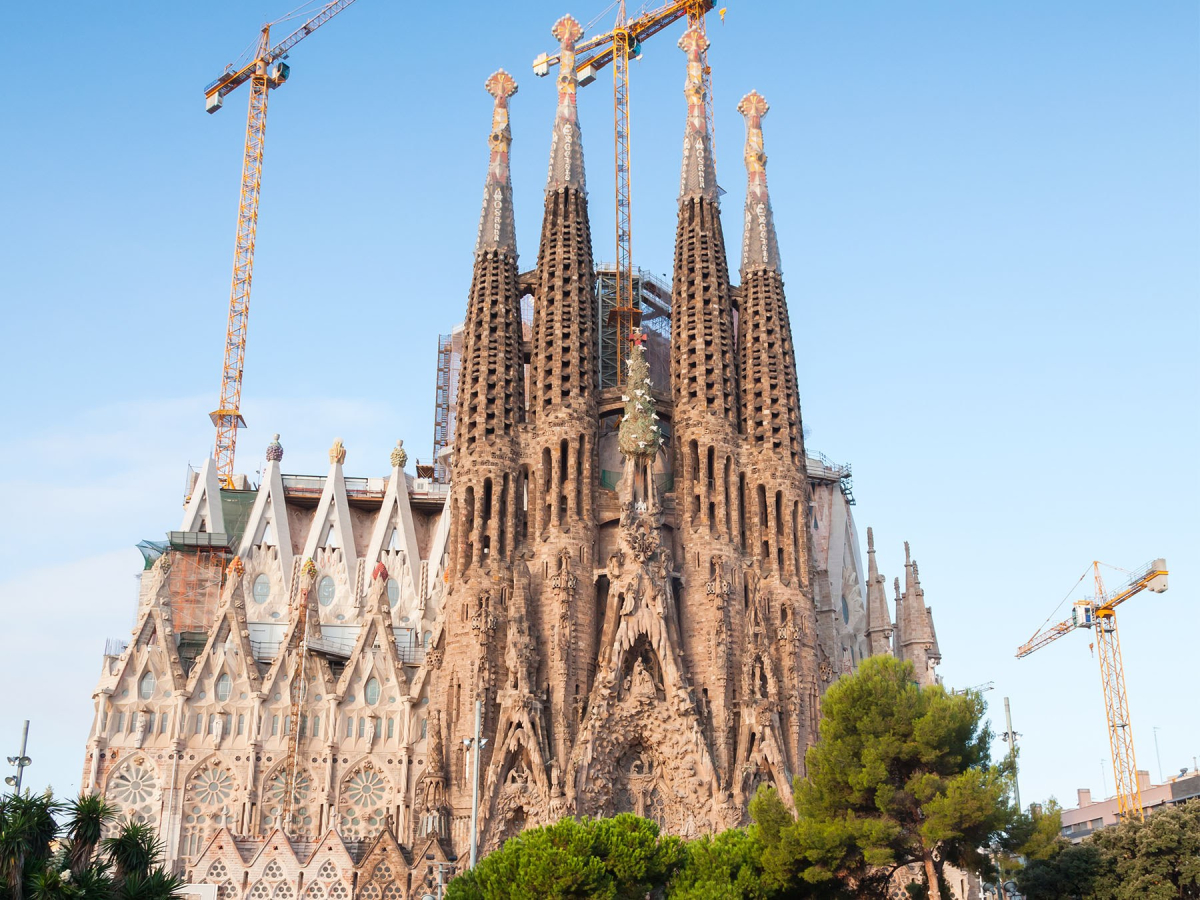
Recognised across construction
A high level of customer service
The world's first carbon neutral training centre
The largest precast concrete installation specialist in the UK
Interlocking Aluminium Crane Mats & Outrigger Pads
Temporary Safety Hole Covers for Construction
Alternative Shuttering Method
Stacker Packers, our engineered levelling shim with a high compressive strength
Safe, fast and cost-effective drilling
Construction’s Fastest Inflatable System
Permanent shuttering solution for hollowcore unit ends
The safe lightweight block moving system
April 18, 2024
Using our purpose-built bending test rig, we compared the material stiffness of two types of crane mats, under three-point loads ranging from 1-tonne up to 3.5-tonne. We tested our own ALIMATS® system made from an extruded aluminium against a commonly used industry competing plastic system made from Ultra High Molecular Weight Polyethylene (UHMW-PE).
On top of each mat, we placed a custom made 30mm deep steel plate, measuring 500mm x 500mm. The purpose of the plate was to simulate site conditions and how the load would be applied from a typical mobile crane outrigger. Equal pressure via the rams was applied simultaneously to each module.
We recorded the deflection in each mat at every phase of the test to highlight the importance of crane mat material stiffness. The tests produced some very interesting results as the loads were applied.
The test we carried out was simulating the mats working as a simply supported beam with a point load applied at mid span. Even though this is not simulating the mat being in contact with the ground, we felt this would be the best test to measure material stiffness – something which is paramount to the performance of load spreader mats working under high load (i.e. mobile crane outriggers).
Here are the results of the first test.
Test 1 – 1 tonne bending test
Deflection recorded under the load was 2mm
It’s important to grasp that the key function of load spreader mats is to reduce the applied pressure to the ground to make sure that the machine and the lift remain stable. This can only happen if the mats are stiff enough, otherwise the load will triangulate straight through them.
We believe the industry is being misled by crane mat manufacturers quoting unrealistic Safe Working Loads (SWL’s), which is one of the reasons we did the bending tests. Most competing systems talk about the compressive strength of the mat material, but not the stiffness – which is a complete red herring and should be challenged, especially when you consider some of the claims being made – whereby plastic systems (which is an inherently flexible material) are quoting SWL values double that of stiffer Aluminium systems.
What some manufacturers are doing is simulating their projects on ground so hard that the mat material is only working in compression – forcing the applied load over a small, concentrated area directly below the crane outrigger. This is misleading the industry, and not safe.
We’ve invested in years of independent research and technical analysis into crane mat material stiffness and read multiple design guides. Take the Construction Ground Condition for Plant, October 2014. It talks about two types of crane mat properties – Strength and Stiffness, with the most important being stiffness.
The hierarchy for the strength and stiffness of crane mat materials, is here:
Strength hierarchy: Steel, Aluminium, Nylon, Polyethylene, Timber
Stiffness hierarchy: Steel, Aluminium, Timber, Nylon, Polyethylene
The drawback with plastic crane mats (UHMW-PE or HDPE) is they have the lowest stiffness properties and are not rigid enough to spread load. Therefore, the load bearing surface below the mats is supporting an applied pressure it is not capable of, which could lead to a catastrophic failure of the lift.
In our opinion plastic mats should not be used as crane mats – or simply put, plastic mats are not fit for purpose. Our justification is shown here with our two other bending tests.
Test 2 – 2.25 tonne bending test
Deflection recorded under the load was 328mm
Deflection recorded under the load was 3mm
Test 3 – 3.5 tonne bending test
Deflection recorded under the load was 161mm
Deflection recorded under the load was 8mm
As you can see from the videos, all three bending tests show significant deflection with the plastic system having reached their elastic limit in all cases. The tests are actually simulating very small loads when you consider typical outrigger loads from mobile cranes, which is even more alarming. From the deflection recorded, the only assumption that can be concluded is that in normal conditions the load simply triangulates through plastic mats. This is also indicated from the gap that appears between the 30mm thick steel plate and the plastic mat during the tests.
This highlights some of the questionable claims made about plastic systems. We don’t dispute the compression properties of plastic mats, but how can they be spreading loads with such poor and inadequate stiffness properties?
Crane mats are made from steel, aluminium, nylon, polyethylene and timber – and they all have high compressive strength. But not all crane mats are stiff – and that matters a lot.
We sometimes use the analogy of a beam or bridge to describe the function of crane outrigger mats. With a rope bridge, it’s probably fair to say it’s strong, but it isn’t stiff. A road bridge on the other hand is strong and stiff, which is why vehicles can safely drive across it. In some respects, outrigger mats are similar to a road bridge in the properties needed for them to perform.
There also appears to be a misconception in the industry when doing lifts on concrete or tarmac that crane mats aren’t necessary because it’s a hard surface. But for an engineer and their Temporary Works Design, they may have to determine what sits below this layer, which could be very soft ground. That’s why crane spreader mats have to be stiff. The tarmac may be solid for the first 3-inches or so, but what lies underneath – a pipe network, landfill or soft peat? What drives a Temporary Works Design may not always be obvious, and this is why they should always be followed. Prior research or site surveys may have already determined the requirement, so to assume the supporting ground is safe because it looks safe, is foolhardy. That’s why tough questions have to be asked and that the Temporary Works Design should always be respected.
On tarmac and concrete you will also want the intermediate compressible layer such as Ethafoam between the crane outriggers and the ground to help improve load distribution and lower ground bearing pressures. Again, without it, the load will triangulate straight through the mats, irrespective of the outrigger mat material.
What we’re really starting to see with enquiries coming from end users, main contractors, appointed persons and engineers is they’re asking specifically for the ALIMATS® system – they’re not asking for crane mats. This tells us the industry is firing up to ask more probing questions around what lies below the ground, the surrounding area and realistic SWL’s.
We’ve recently completed more in-depth research into Safe Working Loads (SWL’s). Working alongside one of the industry’s most qualified and experienced external consulting engineers, we’ve finished first principal analysis enabling us to calculate and recommend SWL’s for:
This will allow us to quote realistic SWL’s to Temporary Works Engineers and Appointed Persons.
We also now have example calculations which showcase how we justify SWL’s. What we’ve learned is that engineers have different interpretations. There are design guides and recommendations on how this work should be followed, but we believe a lot of it is out of date.
Plastic mats (HDPE or UHMW-PE) are not stiff enough to perform as crane outrigger mats. The supporting ground is doing the hard work by taking the load – not the mats. Plastic is stronger than timber, but timber is stiffer.
There are different arguments with timber systems. Bulky and heavy, they can only be moved about using machinery. Unless timber mats are new at the time of use, their structural properties can’t be known due to water absorption and repeatedly being used outdoors in all weathers.
Systems such as steel, are stiff and strong but like timber they are big and weighty, relying on equipment for positioning and manoeuvring.
Our own system has limitations – but this boils down to the size of the crane the mats are going under. Generally speaking, ALIMATS® sit comfortably under cranes up to 150 tonne. The entire interlocking range of aluminium mats from our mini to our extra-long, are light enough for two operatives to pick up by hand, position directly under the cranes outriggers and realign. Not all aluminium mats on the market are handleable – some competing systems are still too heavy to move by hand even when they are fitted with handles.
The ALIMATS® system at a glance
If you’d like to trial ALIMATS® for your next load spread or load transfer project, please get in touch on 01355 345111 or email enquiries@brilliantideasltd.co.uk
You’re a guest user that’s not logged in.